News
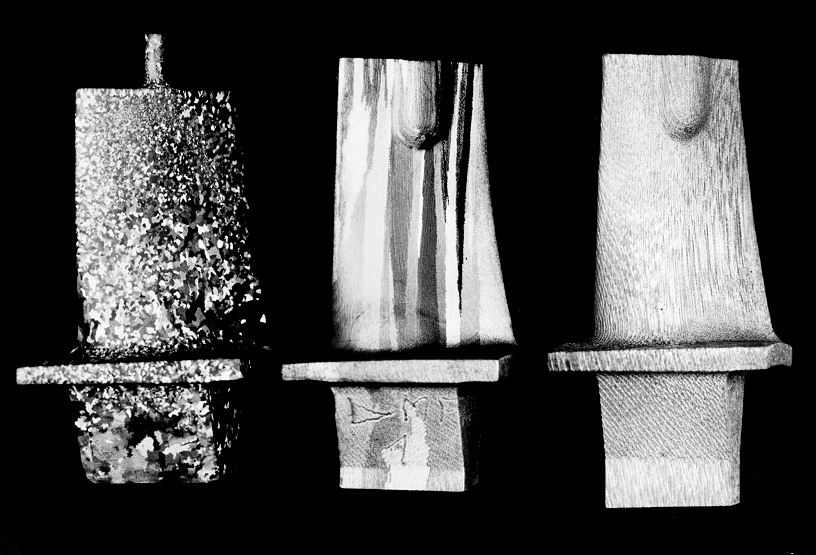
Compte rendu de la journée scientifique sur les superalliages base nickel organisée par la commission Matériaux
Les superalliages base nickel sont aujourd’hui les matériaux métalliques stratégiques et indispensables pour répondre au défi des hautes températures dans les composants structuraux fortement sollicités sur le plan mécanique. C’est en particulier le cas des turbines fournissant de l’énergie ou les forces de propulsion aéronautique, machines combinant conditions de sollicitations thermomécaniques extrêmes et très longues durées de fonctionnement tout en garantissant un haut niveau de fiabilité.
Une journée scientifique a été organisée sur ces alliages bien particuliers par la Commission Technique « Matériaux » le 16 juin dernier à l’ONERA – Châtillon avec l’ambition de dresser un état de l’art académique et industriel sur ces matériaux mais aussi de réfléchir aux perspectives de recherche restant ouvertes sur ce thème.
8 exposés se sont succédé en suivant cette ligne directrice au fil de la journée qui s’est terminée par une table ronde.
1. Introduction et évolution des superalliages base Ni dans les turboréacteurs. J.-Y. Guédou (Safran AE)
2. Métallurgie physique des superalliages base Ni.
L. Nazé (Mines Paris Tech - Evry)
3. Superalliages : Elaboration par voie lingot et poudres. Transformation en demi produits. A. Devaux (Aubert & Duval)
4. Superalliages forgés : application aux disques et spécifications. J.-M. Franchet (Safran)
5. Microstructures / Gammes de forge. N. Bozzolo (Mines Paris Tech – Sophia Antipolis)
6. Les superalliages monocristallins pour aubes de turbine. P. Caron (ONERA)
7. Mécanique et environnement dans les superalliages forgés. E. Andrieu (CIRIMAT)
8. Un exemple de longévité dans les superalliages : l’INCO718. A. Pineau (consultant)
[[{"fid":"2494","view_mode":"default","fields":{"format":"default","field_file_image_alt_text[und][0][value]":"","field_file_image_title_text[und][0][value]":""},"type":"media","link_text":null,"attributes":{"height":191,"width":540,"class":"media-element file-default"}}]]
Les superalliages base Nickel utilisés depuis un siècle ont connu d’énormes progrès au cours des cinquante dernières années, tant sur le plan des compositions chimiques que celui de la maîtrise des microstructures, associée au développement de procédés de mise en œuvre toujours plus performants et efficaces. Cela a permis d’atteindre aujourd’hui un niveau de maturité remarquable et de satisfaire les défis techniques évoqués précédemment en termes de résistance thermique et mécanique.
Cela a été évoqué dans le 1er exposé introductif qui montre que ces matériaux constituent environ la moitié de la masse d’un turboréacteur.
L’explication de la remarquable résistance à haute température de ces alliages est aujourd’hui bien connue : les superalliages présentent des précipités durcissants et stables à haute température de type Ni3Al qui s’opposent à la déformation puisqu’ils doivent être contournés ou cisaillés lorsqu’on déforme le matériau, en fonction de leurs tailles, de leurs taux et aussi de la température comme l’a explicité le 2ème exposé.
L’élaboration et la transformation de ces alliages ont été décrites lors du 3ème exposé : il y a une voie conventionnelle, privilégiée car plus économique, où on fabrique un lingot en plusieurs fusions, qui est ensuite mécaniquement transformé en billettes dans lesquelles des lopins sont découpés destinés à des pièces forgées. L’autre voie est celle de la métallurgie des poudres où de fines gouttelettes de métal liquide sont solidifiées sous forme de poudres qui sont ensuite consolidées.
Cette voie est plus onéreuse et réservée aux alliages plus chargés en éléments durcissants. Elle permet d’obtenir un matériau chimiquement plus homogène en s’affranchissant des problèmes de ségrégation. Dans tous les cas, les procédés d’élaboration sont complexes avec de nombreux paramètres clés à maîtriser pour limiter voire éliminer les défauts qui contrôlent les propriétés d’usage. Les disques de turboréacteurs figurent parmi les pièces les plus critiques.
Le 4ème exposé a permis d’appréhender les modes d’endommagement de ces pièces en relation avec les conditions d’utilisation (fatigue oligocyclique, fissuration, fluage) et la très forte influence des microstructures granulaires sur ces mécanismes de dégradation.
[[{"fid":"2495","view_mode":"default","fields":{"format":"default","field_file_image_alt_text[und][0][value]":"","field_file_image_title_text[und][0][value]":""},"type":"media","link_text":null,"attributes":{"height":296,"width":540,"class":"media-element file-default"}}]]
Les microstructures des pièces forgées dépendent directement des traitements thermo- mécaniques qui sont soigneusement définis, aujourd’hui avec l’aide de modélisations performantes. Les mécanismes qui pilotent les évolutions des grains (taille, morphologie) et les modes d’écrouissage associés, qui contribuent au premier niveau à la résistance du matériau, ont été présentés dans le 5ème exposé : des phénomènes complexes de recristallisation ou de croissance anormale de grains peuvent maintenant être prédits par des modèles de plus en plus affinés à différentes échelles.
[[{"fid":"2496","view_mode":"default","fields":{"format":"default","field_file_image_alt_text[und][0][value]":"","field_file_image_title_text[und][0][value]":""},"type":"media","link_text":null,"attributes":{"height":367,"width":540,"class":"media-element file-default"}}]]
Les aubes de turbine, pièces les plus chaudes des turboréacteurs, sont aujourd’hui fabriquées en superalliage base nickel coulé et solidifié en structure sans joints de grains, c’est-à-dire monocristalline.
[[{"fid":"2497","view_mode":"default","fields":{"format":"default","field_file_image_alt_text[und][0][value]":"","field_file_image_title_text[und][0][value]":""},"type":"media","link_text":null,"attributes":{"height":319,"width":540,"class":"media-element file-default"}}]]
Le 6ème exposé a retracé l’évolution de la fonderie de superalliages depuis la solidification de grains équiaxes jusqu’au mono-grain en passant par les structures à grains colonnaires.
Les compositions chimiques ont évolué ces dernières décennies avec l’introduction d’éléments réfractaires très coûteux comme le rhénium ou les platinoïdes en particulier le ruthénium. Le développement de modèles thermodynamiques ainsi que les approches du type réseaux neuronaux apportent une aide au choix des compostions adaptées aux applications mais la complexité de ces alliages et la multitude de critères à respecter rendent l’expérimentation indispensable.
Depuis leurs premières utilisations au début du 20ème siècle, les alliages de nickel ont été mis en œuvre dans des environnements agressifs (corrosif et/ou oxydant). Ces alliages ont dès l’origine contenu de fortes teneurs en chrome pour répondre à ce problème, teneurs qui ont été fortement réduites dans les derniers développements.
Le 7ème exposé a développé les effets d’environnement (oxygène, eau) sur les superalliages. Il est observé que l’état mécanique local contrôle l’amplitude des effets d’environnement : les instabilités plastiques (effet PLC) inhibent l’effet néfaste de l’oxydation inter-granulaire mais les vitesses de propagation le long des joints de grains ne s’expliquent pas uniquement par la cinétique d’oxydation.
Le 8ème et dernier exposé s’intéressait au superalliage de loin le plus utilisé qui est l’INCO718, alliage durci par une autre famille de précipités, Ni3Nb, ce qui lui confère des propriétés particulières recherchées par l’industriel : la possibilité de modifier les microstructures par traitements thermomécaniques en adéquation avec les propriétés mécaniques recherchées en fait le candidat idéal pour une multitude d’applications en dessous de 650°C, qui est la température au-delà de laquelle ses performances se dégradent.
[[{"fid":"2498","view_mode":"default","fields":{"format":"default","field_file_image_alt_text[und][0][value]":"","field_file_image_title_text[und][0][value]":""},"type":"media","link_text":null,"attributes":{"height":244,"width":540,"class":"media-element file-default"}}]]
Il est largement utilisé dans le domaine aéronautique mais aussi dans d’autres industries (chimique, nucléaire, pétrolière…) et bien qu’étudié depuis 50 ans, il fait encore l’objet de nombreux travaux de recherche, des voies d’optimisation restant encore ouvertes.
La journée s’est terminée par une table ronde où des discussions sur le devenir de ces matériaux ont été engagées. S’il semble qu’ils sont irremplaçables pour longtemps encore dans les pièces très chargées à moyenne température (jusqu’à 750°C) comme les disques, ils sont sans doute proches de leur capacité maximale pour les applications à très hautes températures, au delà de 1200°C, pour lesquelles il faudrait envisager des solutions de matériaux non métalliques, c’est-à-dire céramiques ou intermétalliques réfractaires, dont le niveau de maturité est cependant encore très bas. ?
Aucun commentaire
Vous devez être connecté pour laisser un commentaire. Connectez-vous.